En los aspectos que realmente importan, establecer jerarquías resulta imposible —o, al menos, desaconsejable—. El corazón no es más importante que el cerebro; la vitamina C no es menos indispensable para la salud humana que la vitamina D. El suministro de alimentos y energía, las dos necesidades existenciales tratadas en los artículos anteriores, sería impensable sin la movilización a gran escala de numerosos materiales fabricados por el hombre —metales, aleaciones, compuestos no metálicos y sintéticos—. Lo mismo que ocurre con todos nuestros edificios, infraestructuras, y modos de transporte y comunicación. Sin embargo, esto no parecería evidente si uno juzgara la importancia de estos materiales por la atención que reciben (o más bien no reciben), no solo en los “noticieros” de los medios masivos, sino incluso en los análisis económicos supuestamente más prestigiosos o en las previsiones de desarrollos destacados.
Toda esta cobertura trata abrumadoramente sobre fenómenos inmateriales e intangibles, como el porcentaje anual de crecimiento del PIB (¡cómo solían admirar los economistas occidentales las tasas de dos dígitos de China!), el aumento de las proporciones de deuda nacional (irrelevantes según la Teoría Monetaria Moderna, que considera ilimitada la oferta de dinero), las cifras récord invertidas en nuevas ofertas públicas iniciales (para invenciones tan existencialmente críticas como las aplicaciones de juegos), los beneficios de una conectividad móvil sin precedentes (esperando las redes 5G como si se tratara de la segunda venida) o las promesas de la inteligencia artificial transformando nuestras vidas de manera inminente (la pandemia fue una excelente demostración del vacío absoluto de tales afirmaciones).
Lo primero es lo primero
Podríamos tener una civilización avanzada y razonablemente próspera, capaz de proveer abundancia de alimentos, comodidades materiales y acceso a la educación y la atención sanitaria, sin necesidad de semiconductores, microchips o computadoras personales: de hecho, existió hasta, respectivamente, mediados de la década de 1950 (primeras aplicaciones comerciales de transistores), principios de los años 70 (los primeros microprocesadores de Intel) y principios de los 80 (la propiedad a mayor escala de ordenadores personales).1 Y logramos, hasta la década de 1990, integrar economías, movilizar las inversiones necesarias, construir infraestructuras esenciales y conectar el mundo mediante aviones de fuselaje ancho, sin teléfonos inteligentes, redes sociales ni aplicaciones pueriles. Pero ninguno de estos avances en electrónica y telecomunicaciones habría sido posible sin la provisión asegurada de las energías y materiales requeridos para materializar los inventos en una miríada de componentes, dispositivos, ensamblajes y sistemas que consumen electricidad, desde diminutos microprocesadores hasta enormes centros de datos.
El silicio (Si), procesado en finas obleas (el sustrato básico de los microchips), es el material emblemático de la era electrónica, pero miles de millones de personas podrían vivir prósperamente sin él; no es una limitación existencial para la civilización moderna.
La producción de grandes cristales de silicio de alta pureza (99,999999999 por ciento puro) que se cortan en obleas es un proceso complejo, de múltiples etapas y altamente intensivo en energía: requiere dos órdenes de magnitud más de energía primaria que fabricar aluminio a partir de bauxita, y tres órdenes de magnitud más que fundir hierro y producir acero.2
Sin embargo, la materia prima es súper abundante (el silicio es el segundo elemento más común en la corteza terrestre, representando cerca del 28 por ciento, comparado con el 49 por ciento del oxígeno), y la producción anual de silicio de grado electrónico es muy pequeña en comparación con otros materiales indispensables, alcanzando recientemente un volumen cercano a las 10.000 toneladas de obleas.3
Por supuesto, el consumo anual de un material no es el mejor indicador de su indispensabilidad, pero en este caso el veredicto es claro: por útiles y transformadores que hayan sido los avances electrónicos posteriores a 1950, no constituyen los fundamentos materiales indispensables de la civilización moderna. Y aunque no es posible establecer un orden incuestionable de nuestras necesidades materiales basado en afirmaciones de su importancia, puedo ofrecer una clasificación defendible que considera su indispensabilidad, ubicuidad y la magnitud de su demanda. Cuatro materiales destacan en esta escala combinada y forman lo que he denominado los cuatro pilares de la civilización moderna: cemento, acero, plásticos y amoníaco.4
Física y químicamente, estos cuatro materiales se distinguen por una enorme diversidad de propiedades y funciones. Sin embargo, a pesar de estas diferencias en atributos y usos específicos, comparten algo más que su indispensabilidad para el funcionamiento de las sociedades modernas. Su demanda es mayor (y sigue creciendo) que la de otros insumos esenciales. En 2019, el mundo consumió aproximadamente 4500 millones de toneladas de cemento, 1800 millones de toneladas de acero, 370 millones de toneladas de plásticos y 150 millones de toneladas de amoníaco, y no son fácilmente sustituibles por otros materiales, al menos no en un futuro cercano ni a escala global.5
Como se mencionó en el artículo dedicado a la producción de alimentos, solo un reciclaje absolutamente completo de todos los desechos generados por los animales de pastoreo podría, junto con un reciclaje casi perfecto de todas las demás fuentes de nitrógeno orgánico, proporcionar la cantidad de nitrógeno que se aplica anualmente a los cultivos en forma de fertilizantes basados en amoníaco. Al mismo tiempo, no existen materiales que puedan rivalizar con la combinación de maleabilidad, durabilidad y ligereza que ofrecen muchos tipos de plásticos.6 De manera similar, aunque fuésemos capaces de producir masas idénticas de madera para construcción o piedra de cantera, estas no igualarían la resistencia, versatilidad y durabilidad del hormigón armado. Podríamos construir pirámides y catedrales, pero no elegantes puentes arqueados de gran longitud, gigantescas presas hidroeléctricas, carreteras de varios carriles o largas pistas de aeropuertos. Y el acero se ha vuelto tan ubicuo que su despliegue insustituible determina nuestra capacidad para extraer energías, producir alimentos y proporcionar refugio a las poblaciones, así como garantizar la extensión y calidad de todas las infraestructuras esenciales: ningún otro metal podría, ni remotamente, convertirse en su sustituto.
Otro aspecto clave que comparten estos cuatro materiales resulta particularmente relevante al considerar un futuro sin carbono fósil: la producción a gran escala de todos ellos depende en gran medida de la combustión de combustibles fósiles, y algunos de estos también sirven como materia prima para la síntesis de amoníaco y la producción de plásticos. La fundición de mineral de hierro en altos hornos requiere coque producido a partir de carbón (y también gas natural); la energía para la producción de cemento proviene principalmente de polvo de carbón, coque de petróleo y fueloil pesado.
La gran mayoría de las moléculas simples que se enlazan en largas cadenas o ramificaciones para formar plásticos se derivan del petróleo crudo y el gas natural. Además, en la síntesis moderna de amoníaco, el gas natural se utiliza tanto como fuente de hidrógeno como de energía para el procesamiento.
Como resultado, la producción global de estos cuatro materiales indispensables representa aproximadamente el 17% del suministro mundial de energía primaria y el 25% de todas las emisiones de CO2 originadas en la combustión de combustibles fósiles. Actualmente no existen alternativas comercialmente disponibles y fácilmente implementables a gran escala que puedan sustituir estos procesos establecidos.7 Aunque no faltan propuestas y técnicas experimentales para producir estos materiales sin depender del carbono fósil —que van desde nuevas catalizaciones para la síntesis de amoníaco hasta la fabricación de acero basada en hidrógeno—, ninguna de estas alternativas ha sido comercializada. Incluso, si se emprendiera una búsqueda agresiva de opciones no basadas en carbono, sería evidente que tomaría décadas reemplazar las capacidades existentes, que producen a precios asequibles y a tasas anuales de cientos de millones a miles de millones de toneladas.8
Para apreciar realmente la importancia de estos materiales, explicaré sus propiedades y funciones básicas, esbozaré brevemente las historias de los avances técnicos y las invenciones decisivas que los hicieron abundantemente disponibles y asequibles, y describiré la enorme variedad de sus usos modernos. Comenzaré con el amoníaco, debido a su carácter indispensable para alimentar a una proporción creciente de la población mundial, y continuaré, en el orden de la producción mundial anual en masa, con los plásticos, el acero y el cemento.
Amoníaco: el gas que alimenta al mundo
De las cuatro sustancias (y a pesar de mi aversión a los rankings), el amoníaco merece ocupar el primer lugar como nuestro material más importante. Como se explicó en el artículo anterior, sin su uso como el principal fertilizante nitrogenado (ya sea directamente o como materia prima para la síntesis de otros compuestos nitrogenados), sería imposible alimentar al menos al 40% y hasta el 50% de los casi 8000 millones de personas que habitan el planeta hoy en día. Dicho de otra manera: en 2020, casi 4000 millones de personas no habrían estado vivas sin el amoníaco sintético. Ninguna de las limitaciones existenciales comparables se aplica a los plásticos o al acero, ni al cemento que se requiere para fabricar concreto (ni, como ya se mencionó, al silicio).
El amoníaco es un compuesto inorgánico simple formado por un átomo de nitrógeno y tres de hidrógeno (NH3), lo que significa que el nitrógeno constituye el 82% de su masa.9 A presión atmosférica, es un gas invisible con un característico olor penetrante que recuerda a inodoros sin descargar o a estiércol animal en descomposición. Inhalarlo en bajas concentraciones puede causar dolores de cabeza, náuseas y vómitos; en concentraciones más altas, irrita los ojos, la nariz, la boca, la garganta y los pulmones; y la inhalación de concentraciones muy altas puede ser instantáneamente fatal. En contraste, el ion amonio (NH4+), formado por la disolución del amoníaco en agua, no es tóxico y no penetra fácilmente las membranas celulares.
Sintetizar esta simple molécula resultó ser sorprendentemente desafiante. La historia de los inventos incluye casos famosos de descubrimientos accidentales; en este capítulo sobre materiales, la historia del Teflón podría ser el ejemplo más apropiado. En 1938, Roy Plunkett, un químico de DuPont, y su asistente Jack Rebok formularon el tetrafluoroetileno como un nuevo compuesto refrigerante. Después de almacenarlo en cilindros refrigerados, descubrieron que el compuesto sufrió una inesperada polimerización, convirtiéndose en politetrafluoroetileno, un polvo blanco, ceroso y resbaladizo.
Después de la Segunda Guerra Mundial, el Teflón se convirtió en uno de los materiales sintéticos más conocidos y, quizás, el único que llegó al argot político (hemos tenido presidentes Teflón, pero aparentemente no presidentes Bakelita—aunque hubo una Dama de Hierro).10
La síntesis de amoníaco a partir de sus elementos pertenece a una categoría opuesta de descubrimientos: aquellos con un objetivo claramente definido, perseguidos por algunos de los científicos más capacitados y finalmente alcanzados por un investigador perseverante. La necesidad de este avance era evidente. Entre 1850 y 1900, la población total de los países industrializados de Europa y América del Norte creció de 300 a 500 millones, y la rápida urbanización impulsó una transición dietética desde un suministro apenas adecuado basado en cereales hacia una ingesta energética mayor, que incluía más productos animales y azúcar.11 Las cosechas seguían siendo limitadas, pero el cambio dietético se sostuvo gracias a una expansión sin precedentes de las tierras de cultivo: entre 1850 y 1900, unos 200 millones de hectáreas de pastizales en América del Norte y del Sur, Rusia y Australia fueron convertidos en campos de cereales.12
La maduración de la ciencia agronómica dejó en claro que la única forma de garantizar alimentos suficientes para las crecientes poblaciones del siglo XX era aumentar los rendimientos mediante el incremento del suministro de nitrógeno y fósforo, dos macronutrientes esenciales para las plantas. La extracción de fosfatos (primero en Carolina del Norte y luego en Florida) y su tratamiento con ácidos abrió el camino a un suministro confiable de fertilizantes fosfatados.13 Sin embargo, no existía una fuente de nitrógeno igualmente asegurada. La extracción de guano (excrementos acumulados de aves, moderadamente ricos en nitrógeno) en islas tropicales secas agotó rápidamente los depósitos más ricos, y las crecientes importaciones de nitratos chilenos (el país posee extensas capas de nitrato de sodio en sus regiones áridas del norte) eran insuficientes para satisfacer la futura demanda global.14
El desafío consistía en garantizar que la humanidad pudiera asegurar suficiente nitrógeno para sostener su creciente población. Esta necesidad fue explicada de la manera más clara posible en 1898 por William Crookes, químico y físico, durante su discurso presidencial ante la Asociación Británica para el Avance de la Ciencia, dedicado al llamado problema del trigo. Crookes advirtió que “todas las naciones civilizadas están en grave peligro de no tener suficiente para comer,” pero vislumbró una solución: la ciencia vendría al rescate, aprovechando la masa prácticamente ilimitada de nitrógeno en la atmósfera (presente como la molécula no reactiva N2) y convirtiéndolo en compuestos asimilables por las plantas. Concluyó acertadamente que este desafío “difiere materialmente de otros descubrimientos químicos que están en el aire, por así decirlo, pero aún no se han concretado. La fijación del nitrógeno es vital para el progreso de la humanidad civilizada. Otros descubrimientos contribuyen a nuestro mayor confort intelectual, lujo o conveniencia; sirven para facilitar la vida, acelerar la adquisición de riqueza o ahorrar tiempo, salud o preocupaciones. La fijación del nitrógeno es una cuestión del futuro no muy lejano.”15
La visión de Crookes se materializó apenas diez años después de su discurso. La síntesis de amoníaco a partir de sus elementos, nitrógeno e hidrógeno, fue un objetivo perseguido por varios químicos altamente cualificados (entre ellos Wilhelm Ostwald, ganador del Premio Nobel de Química en 1909). Sin embargo, en 1908, Fritz Haber —entonces profesor de química física y electroquímica en la Technische Hochschule de Karlsruhe— junto con su asistente inglés Robert Le Rossignol y con el apoyo de BASF, la principal empresa química de Alemania (y del mundo), fue el primer investigador en lograrlo.16 Su solución se basó en el uso de un catalizador de hierro (un compuesto que acelera una reacción química sin alterar su propia composición) y en la aplicación de una presión de reacción sin precedentes.
Escalar el éxito experimental de Haber a un nivel comercial no fue un desafío menor. Bajo el liderazgo de Carl Bosch, un experto en ingeniería química y metalúrgica que se unió a BASF en 1899, el éxito se alcanzó en tan solo cuatro años. La primera planta del mundo de síntesis de amoníaco comenzó a operar en Oppau en septiembre de 1913, y el término “proceso Haber-Bosch” ha perdurado desde entonces.17
En menos de un año, el amoníaco producido en la planta de Oppau fue desviado para fabricar nitrato destinado a producir explosivos para el ejército alemán. Una nueva fábrica de amoníaco, mucho más grande, se completó en 1917 en Leuna, pero esto tuvo poco efecto para evitar la derrota de Alemania. La expansión de la síntesis de amoníaco continuó tras la guerra, a pesar de la crisis económica de los años 30, y siguió durante la Segunda Guerra Mundial. Sin embargo, para 1950, el amoníaco sintético seguía siendo mucho menos común que los estiércoles animales.18
Las dos décadas siguientes vieron un aumento de ocho veces en la producción de amoníaco, superando las 30 millones de toneladas al año, ya que los fertilizantes sintéticos hicieron posible la Revolución Verde (que comenzó durante la década de 1960): la adopción de nuevas variedades superiores de trigo y arroz que, al recibir cantidades adecuadas de nitrógeno, lograron rendimientos sin precedentes. Las principales innovaciones detrás de este aumento fueron el uso de gas natural como fuente de hidrógeno y la introducción de compresores centrífugos eficientes y mejores catalizadores.19
Luego, como en tantos otros casos de desarrollo industrial moderno, la China posterior a Mao tomó la delantera. Mao fue responsable de la hambruna más mortífera de la historia (1958–1961), y cuando murió en 1976, el suministro de alimentos per cápita del país apenas era mejor que cuando proclamó la existencia del Estado comunista en 1949.20 El primer gran acuerdo comercial de China tras el viaje del presidente Nixon a Pekín en 1972 fue un pedido de 13 de las plantas de amoníaco-urea más avanzadas del mundo a M. W. Kellogg, de Texas.21 Para 1984, el país abolió el racionamiento de alimentos en las ciudades y, para el año 2000, el suministro diario promedio de alimentos por persona en China era mayor que el de Japón.22
La única forma de lograr esto fue superando la barrera del nitrógeno del país y elevando la cosecha anual de cereales a más de 650 millones de toneladas al año. El mejor análisis de los flujos recientes de nitrógeno en la agricultura de China muestra que alrededor del 60 por ciento del nutriente disponible para los cultivos del país proviene del amoníaco sintético: alimentar a tres de cada cinco personas en China depende, por tanto, de la síntesis de este compuesto.23 La media mundial correspondiente es de aproximadamente el 50 por ciento. Esta dependencia justifica fácilmente considerar la síntesis de amoníaco por el proceso Haber-Bosch como quizás el avance técnico más trascendental de la historia. Otras invenciones, como juzgó correctamente William Crookes, atienden a nuestras comodidades, conveniencias, lujos, riqueza o productividad, y otras aún salvan vidas de muertes prematuras y enfermedades crónicas. Sin embargo, sin la síntesis de amoníaco, no podríamos garantizar la supervivencia misma de grandes proporciones de la población actual y futura.24
Es importante añadir que el 50 por ciento de la humanidad que depende del amoníaco no es una estimación inmutable. Dados los patrones alimentarios y las prácticas agrícolas actuales, el nitrógeno sintético alimenta a la mitad de la humanidad, o, simplemente, la mitad de la población mundial no podría mantenerse sin fertilizantes nitrogenados sintéticos. Pero esa proporción sería menor si el mundo acomodado adoptara una dieta mayoritariamente vegetariana como la india, y sería mayor si todo el mundo comiera tan bien como lo hacen los chinos hoy en día, sin mencionar la adopción universal de la dieta estadounidense.25 También podríamos reducir nuestra dependencia de los fertilizantes nitrogenados disminuyendo el desperdicio de alimentos (como vimos anteriormente) y utilizando los fertilizantes de manera más eficiente.
Aproximadamente el 80 por ciento de la producción mundial de amoníaco se utiliza para fertilizar cultivos; el resto se destina a la fabricación de ácido nítrico, explosivos, propulsores de cohetes, colorantes, fibras, y productos de limpieza para ventanas y suelos.26 Con las precauciones adecuadas y equipos especiales, el amoníaco puede aplicarse directamente a los campos;27 sin embargo, en su mayoría, el compuesto se utiliza como materia prima indispensable para la producción de fertilizantes nitrogenados sólidos y líquidos. La urea, el fertilizante sólido con el mayor contenido de nitrógeno (46 por ciento), predomina.28 Recientemente, ha representado aproximadamente el 55 por ciento de todo el nitrógeno aplicado a los campos del mundo y se emplea ampliamente en Asia para sostener las cosechas de arroz y trigo de China e India, las dos naciones más pobladas del mundo, así como para garantizar buenos rendimientos en otros cinco países asiáticos con más de 100 millones de habitantes.29
Entre los fertilizantes nitrogenados menos importantes se encuentran el nitrato de amonio, el sulfato de amonio, el nitrato de calcio y amonio, así como diversas soluciones líquidas. Una vez que los fertilizantes nitrogenados se aplican a los campos, es casi imposible controlar sus pérdidas naturales debido a la volatilización (de compuestos de amoníaco), la lixiviación (los nitratos son fácilmente solubles en agua) y la desnitrificación (la conversión bacteriana de nitratos nuevamente en moléculas de nitrógeno del aire).30
Actualmente, solo existen dos soluciones directas efectivas para las pérdidas de nitrógeno en los campos: la aplicación de compuestos de liberación lenta, que son costosos; y, de manera más práctica, el uso de la agricultura de precisión, aplicando fertilizantes únicamente cuando se necesiten y basándose en análisis del suelo.31 Como ya se ha señalado, las medidas indirectas —como el aumento de los precios de los alimentos y la reducción del consumo de carne— podrían ser efectivas, pero no son muy populares. En consecuencia, es improbable que cualquier combinación concebible de estas soluciones provoque un cambio radical en el consumo global de fertilizantes nitrogenados. Actualmente se sintetizan alrededor de 150 megatoneladas de amoníaco al año, de las cuales aproximadamente el 80 por ciento se utiliza como fertilizante. Cerca del 60 por ciento de este fertilizante se aplica en Asia, alrededor de una cuarta parte en Europa y América del Norte, y menos del 5 por ciento en África.32
Los países ricos, sin duda, podrían y deberían reducir sus altas tasas de aplicación (su suministro promedio de alimentos per cápita ya es excesivo), y China e India —grandes consumidores— tienen muchas oportunidades de disminuir sus aplicaciones excesivas de fertilizantes.
Sin embargo, África, el continente con el crecimiento poblacional más rápido, sigue estando privado de este nutriente y es un importante importador de alimentos. Cualquier esperanza de lograr una mayor autosuficiencia alimentaria en el continente depende del aumento del uso de nitrógeno: después de todo, el uso reciente de amoníaco en África ha sido menos de un tercio del promedio europeo.33 La mejor solución (y largamente buscada) para aumentar el suministro de nitrógeno sería dotar a las plantas no leguminosas de capacidades para fijar nitrógeno, una promesa que la ingeniería genética aún no ha cumplido, mientras que una opción menos radical —inocular las semillas con bacterias fijadoras de nitrógeno— es una innovación reciente cuyo alcance comercial eventual sigue siendo incierto.
Plásticos: diversos, útiles, problemáticos
Los plásticos constituyen un amplio grupo de materiales orgánicos sintéticos (o semisintéticos) cuya característica común es su aptitud para ser moldeados. La síntesis de plásticos comienza con monómeros, moléculas simples que pueden enlazarse en largas cadenas o ramificaciones para formar polímeros. Los dos monómeros clave, etileno y propileno, se producen mediante el craqueo a vapor (calentamiento a 750-950 ºC) de materias primas hidrocarburadas, y los hidrocarburos también suministran la energía para las síntesis posteriores.34 La maleabilidad de los plásticos permite formarlos mediante moldeo, prensado o extrusión, lo que da lugar a formas que van desde películas delgadas hasta tuberías de alta resistencia, y desde botellas ligerísimas hasta contenedores robustos y masivos para residuos.
La producción mundial está dominada por los termoplásticos, polímeros que se ablandan fácilmente al calentarse y se endurecen nuevamente al enfriarse. El polietileno (PE) de baja y alta densidad representa ahora más del 20 por ciento de los polímeros plásticos del mundo, el polipropileno (PP) aproximadamente el 15 por ciento, y el policloruro de vinilo (PVC) más del 10 por ciento.35 En contraste, los plásticos termoestables (como los poliuretanos, poliamidas, melaminas y la urea-formaldehído) resisten el ablandamiento incluso al calentarse.
Algunos termoplásticos combinan una baja gravedad específica (peso ligero) con una dureza relativamente alta (durabilidad). Aunque el aluminio, material duradero, pesa solo un tercio de lo que pesa el acero al carbono, la densidad del PVC es menos del 20 por ciento y la del PP menos del 12 por ciento en comparación con el acero; mientras que la resistencia máxima a la tracción del acero estructural es de 400 megapascales, la del poliestireno es de 100 megapascales, el doble que la de la madera o el vidrio, y solo un 10 por ciento menor que la del aluminio.36
Esta combinación de bajo peso y alta resistencia ha convertido a los termoplásticos en la opción preferida para aplicaciones como tuberías y bridas de alta resistencia, superficies antideslizantes y tanques químicos. Los polímeros termoplásticos se utilizan ampliamente en interiores y exteriores de automóviles (parachoques de PP, tableros y piezas de PVC, lentes de faros de policarbonato); los termoplásticos ligeros, resistentes a altas temperaturas o retardantes de llama (mezclas de PVC y acrílico, policarbonato) dominan los interiores de las aeronaves modernas; y los plásticos reforzados con fibra de carbono (materiales compuestos) se emplean ahora para la fabricación de fuselajes de aviones.37
Los primeros plásticos, en particular el celuloide hecho de nitrato de celulosa y alcanfor (más tarde, el material altamente inflamable principal de la industria cinematográfica, desplazado recién en la década de 1950), se produjeron en pequeñas cantidades durante las últimas tres décadas del siglo XIX. Sin embargo, el primer material termoestable (moldeado a 150-160 ºC) fue creado en 1907 por Leo Hendrik Baekeland, un químico belga que trabajaba en Nueva York.38 Su empresa, General Bakelite Company, fundada en 1910, fue la primera productora industrial de un plástico que se moldeaba en piezas que iban desde aislantes eléctricos hasta teléfonos de disco negro. Durante la Segunda Guerra Mundial, se utilizó en componentes de armas ligeras. Por otro lado, Jacques Brandenberger inventó el celofán en 1908.
Durante el período de entreguerras surgieron las primeras síntesis a gran escala de PVC, descubierto ya en 1838, pero nunca utilizado fuera del laboratorio. En este tiempo, empresas como DuPont en los Estados Unidos, Imperial Chemical Industries (ICI) en el Reino Unido e IG Farben en Alemania financiaron (con gran éxito) investigaciones dirigidas al descubrimiento de nuevos materiales plásticos.39 Antes de la Segunda Guerra Mundial, esto resultó en la producción comercial de acetato de celulosa (hoy en paños y toallitas absorbentes), neopreno (goma sintética), poliéster (para tejidos y tapicería), y polimetilmetacrilato (plexiglás, ahora aún más común gracias al resurgimiento de divisores y pantallas protectoras inducido por la COVID). El nailon, producido desde 1938, tuvo como primeros productos comerciales cerdas de cepillos de dientes y medias; hoy en día se utiliza en redes de pesca, paracaídas y otros productos. Como ya se mencionó, también en esa época comenzó la producción de Teflón, el famoso revestimiento antiadherente. La producción asequible de estireno también empezó en los años treinta, y actualmente este material se usa principalmente como poliestireno (PS) en materiales de embalaje y utensilios desechables como vasos y platos.
IG Farben introdujo los poliuretanos en 1937 (espumas para muebles, aislantes); ICI utilizó presiones muy altas para sintetizar polietileno (empleado en embalajes y aislantes) y comenzó a producir metilmetacrilato (para adhesivos, revestimientos y pinturas) en 1933. El tereftalato de polietileno (PET), convertido desde la década de 1970 en uno de los principales residuos del planeta en forma de botellas de bebidas desechadas, fue patentado en 1941 y producido masivamente desde principios de la década de 1950 (la infernal botella de PET fue patentada en 1973).40 Entre las adiciones más destacadas tras la Segunda Guerra Mundial se encuentran los policarbonatos (para lentes ópticos, ventanas, cubiertas rígidas), las poliimidas (para tubos médicos), los polímeros de cristal líquido (principalmente para electrónica), y marcas registradas famosas de DuPont como Tyvek® (1955), Lycra® (1959) y Kevlar® (1971).41
A finales del siglo XX, había 50 tipos diferentes de plásticos en el mercado global, y esta nueva diversidad, junto con la creciente demanda de los compuestos más usados (PE, PP, PVC y PET), condujo a un crecimiento exponencial en la demanda.
La producción mundial de plásticos aumentó de unas 20.000 toneladas en 1925 a 2 millones de toneladas en 1950, 150 millones de toneladas en el año 2000 y aproximadamente 370 millones de toneladas en 2019.42 La mejor manera de apreciar la omnipresencia de los materiales plásticos en nuestra vida diaria es observar cuántas veces al día nuestras manos tocan, nuestros ojos ven, nuestros cuerpos descansan sobre o nuestros pies pisan algo de plástico: ¡podría sorprenderte la frecuencia de estos encuentros! Mientras escribo esto, las teclas de mi portátil Dell y un ratón inalámbrico bajo mi mano derecha están hechos de acrilonitrilo butadieno estireno; estoy sentado en una silla giratoria tapizada con una tela de poliéster, cuyas ruedas de nailon descansan sobre una alfombrilla de policarbonato que cubre una moqueta de poliéster…
Una industria que comenzó suministrando pequeñas piezas industriales (la primera aplicación fue el pomo de la palanca de cambios de un Rolls-Royce de 1916) y diversos objetos domésticos, ha ampliado enormemente esas dos nichos comerciales originales (con la electrónica de consumo añadiendo cada año miles de millones de nuevos artículos dependientes del plástico) y ha incorporado aplicaciones a gran escala que van desde carrocerías de automóviles e interiores completos de aviones hasta tuberías de gran diámetro.
Sin embargo, los plásticos han encontrado sus roles más imprescindibles en la atención sanitaria en general y en el tratamiento hospitalario de enfermedades infecciosas en particular. La vida moderna comienza (en salas de maternidad) y termina (en unidades de cuidados intensivos) rodeada de artículos de plástico.43 Aquellas personas que no comprendían previamente el papel de los plásticos en la atención sanitaria moderna recibieron una lección gracias a la COVID-19. La pandemia nos mostró esta realidad de formas a menudo drásticas, cuando médicos y enfermeros en Norteamérica y Europa se quedaron sin equipos de protección personal (EPP) —guantes desechables, mascarillas, viseras, gorros, batas y cubrezapatos— y los gobiernos compitieron entre sí para transportar en avión suministros limitados (y a precios desorbitados) desde China, donde los productores occidentales, obsesionados con reducir costos, habían trasladado la mayor parte de sus líneas de producción, generando peligrosas y completamente evitables carencias de suministro.44
Los artículos de plástico en hospitales están hechos, sobre todo, de diferentes tipos de PVC: tubos flexibles (utilizados para alimentar pacientes, suministrar oxígeno y monitorizar la presión arterial), catéteres, recipientes intravenosos, bolsas de sangre, envases estériles, bandejas y cubetas, orinales y barandillas de camas, mantas térmicas y una infinidad de utensilios de laboratorio. El PVC es ahora el componente principal de más de una cuarta parte de todos los productos sanitarios, y en los hogares modernos está presente en membranas para paredes y techos, marcos de ventanas, persianas, mangueras, aislamientos de cables, componentes electrónicos, una creciente variedad de artículos de oficina y juguetes, además de tarjetas de crédito para comprar todo lo anterior.45
En los últimos años han crecido las preocupaciones sobre la contaminación por plásticos en la tierra y, aún más, en el océano, las aguas costeras y las playas. Regresaré a este tema en el artículo dedicado al medioambiente, pero este vertido irresponsable de plásticos no es un argumento en contra del uso adecuado de estos materiales sintéticos diversos y, a menudo, verdaderamente imprescindibles. Además, en cuanto a las microfibras, es un error asumir, como hacen muchos, que la mayor parte de su presencia en el agua del océano deriva del desgaste de textiles sintéticos. Esos polímeros ahora representan dos tercios de la producción mundial de fibras, pero un estudio de muestras de agua de mar mostró que las fibras oceánicas son principalmente (>90%) de origen natural.46
El acero: omnipresente y reciclable
Los aceros (el plural es más preciso, ya que existen más de 3500 variedades) son aleaciones dominadas por el hierro (Fe).47 El hierro bruto o fundido, el metal caliente producido en altos hornos, contiene típicamente un 95-97% de hierro, un 1,8-4% de carbono y un 0,5-3% de silicio, con apenas trazas de otros elementos.48 Su alto contenido de carbono lo hace quebradizo, tiene baja ductilidad (la capacidad de estirarse) y su resistencia a la tracción (la capacidad de soportar fuerzas que lo estiran sin romperse) es inferior a la del bronce o el latón.
El acero preindustrial se fabricaba en Asia y Europa mediante diversos métodos artesanales, siempre de manera laboriosa y costosa, por lo que nunca estuvo disponible para usos comunes.49 El acero moderno se obtiene del hierro fundido reduciendo su alto contenido de carbono al 0,08-2,1% en peso. Las propiedades físicas del acero superan con creces las de las piedras más duras y las de los otros dos metales más comunes. El granito tiene una resistencia a la compresión similar (capacidad para soportar cargas que acortan el material), pero su resistencia a la tracción es un orden de magnitud inferior: las columnas de granito soportan cargas tan bien como el acero, pero las vigas de acero pueden soportar cargas 15-30 veces mayores.50
La resistencia a la tracción típica del acero es aproximadamente siete veces mayor que la del aluminio y casi cuatro veces mayor que la del cobre; su dureza es, respectivamente, cuatro y ocho veces superior, y además resiste altas temperaturas: el aluminio se funde a 660 ºC, el cobre a 1085 ºC, y el acero solo a 1425 ºC.
Los aceros se dividen en cuatro categorías principales.51 Los aceros al carbono (el 90% de todos los aceros en el mercado contienen entre un 0,3% y un 0,95% de carbono) se utilizan en una amplia variedad de aplicaciones, desde puentes hasta frigoríficos y desde engranajes hasta tijeras. Los aceros aleados incluyen proporciones variables de uno o más elementos (más comúnmente manganeso, níquel, silicio y cromo, aunque también aluminio, molibdeno, titanio y vanadio), añadidos para mejorar sus propiedades físicas (dureza, resistencia, ductilidad).
El acero inoxidable (10-20% de cromo) se fabricó por primera vez en 1912 para utensilios de cocina, y hoy se usa ampliamente en instrumentos quirúrgicos, motores, piezas de maquinaria y construcción.52 Los aceros para herramientas tienen una resistencia a la tracción de 2 a 4 veces superior a la de los mejores aceros de construcción, y se emplean para cortar acero y otros metales, para troqueles (estampado o extrusión de metales o plásticos), así como para corte manual y martillado. Además, todos los aceros (excepto algunas variedades de inoxidable) son magnéticos, lo que los hace aptos para la fabricación de maquinaria eléctrica.
El acero define el aspecto de la civilización moderna y hace posibles sus funciones más fundamentales. Es el metal más utilizado y forma innumerables componentes críticos, visibles e invisibles, del mundo actual. Además, casi todos los demás productos metálicos y no metálicos que empleamos han sido extraídos, procesados, moldeados, acabados y distribuidos con herramientas y máquinas de acero, y ningún medio de transporte masivo actual podría funcionar sin él. El acero desnudo es omnipresente tanto dentro como fuera de nuestros hogares, en objetos pequeños (cubiertos, cuchillos, ollas, sartenes, utensilios de cocina, herramientas de jardín) y grandes (electrodomésticos, cortacéspedes, bicicletas, coches).
Antes de que se levanten los grandes edificios de las ciudades, es posible observar imponentes máquinas hincadoras de pilotes de acero o de hormigón armado con acero para las cimentaciones, y posteriormente el lugar queda dominado durante meses por altas grúas de construcción de acero. En 1954, el edificio Socony-Mobil de Nueva York fue el primer rascacielos completamente revestido en acero inoxidable, y más recientemente, el Burj Khalifa de Dubái, con 828 metros de altura, emplea paneles de acero inoxidable texturizado y pines tubulares verticales de acero.53
El acero es tanto un componente estructural crítico como un elemento de diseño en muchos puentes elegantes en voladizo y colgantes.54 En el puente Golden Gate de San Francisco, constantemente repintado de naranja,55 el acero es esencial, mientras que el puente Akashi Kaikyō de Japón, con el tramo central más largo del mundo de casi 2 kilómetros, cuenta con torres de acero que sostienen cables de acero trenzado de 1,12 metros de diámetro.56
Las calles de las ciudades están bordeadas de postes de iluminación regularmente espaciados, fabricados con acero galvanizado en caliente y revestido en polvo para resistir la oxidación. Las señales de tráfico y las estructuras para letreros elevados están hechas de acero laminado, y las barreras de protección en las carreteras utilizan acero corrugado. Las torres de acero soportan gruesos cables de acero que transportan a millones de esquiadores cuesta abajo y a visitantes en teleféricos hasta cumbres elevadas. Las torres de radio y televisión (mástiles atirantados) han batido numerosos récords de altura entre las estructuras construidas por el hombre, mientras que los paisajes modernos contienen interminables repeticiones de torres de transmisión eléctrica de alta tensión.
Dos adiciones recientes y destacadas son las altísimas torres atirantadas para transmitir señales de telefonía móvil y los conjuntos de grandes torres de turbinas eólicas, tanto en tierra como en alta mar; además, las estructuras de acero más masivas en el océano son las enormes plataformas de producción de petróleo y gas.57
Por peso, el acero suele ser el componente principal del equipo de transporte. Los aviones comerciales son una notable excepción, ya que los dominan las aleaciones de aluminio y las fibras compuestas, y el acero representa aproximadamente el 10% del peso del avión, principalmente en los motores y el tren de aterrizaje.58 En cambio, un coche promedio contiene alrededor de 900 kilogramos de acero.59 Con una producción mundial anual cercana a los 100 millones de vehículos, esto equivale a unos 90 millones de toneladas de este metal, de las cuales aproximadamente el 60% es acero de alta resistencia que permite reducir entre un 26% y un 40% el peso en comparación con el acero convencional.60 Aunque los trenes de alta velocidad modernos (carrocerías de aluminio, interiores de plástico) contienen solo un 15% de acero (en ruedas, ejes, rodamientos y motores), su funcionamiento requiere vías dedicadas fabricadas con rieles de acero más pesados de lo normal.61
Los cascos de los petroleros, de los transportadores de gas licuado y de los buques de carga a granel que transportan minerales, cereales o cemento están fabricados doblando grandes placas de acero de alta resistencia en las formas deseadas y soldándolas entre sí. Sin embargo, la mayor revolución en el transporte marítimo de la posguerra ha sido el uso de los buques portacontenedores. Estas embarcaciones transportan carga en cajones de acero con dimensiones estandarizadas.62 Estas cajas de acero tienen aproximadamente 2,5 metros de altura y ancho (la longitud varía) y se apilan dentro de los cascos y mucho más alto sobre la cubierta. Es muy probable que todo lo que vistes haya sido transportado hasta su punto de venta final en un contenedor de acero que inició su viaje en una fábrica de Asia.
¿Y cómo se fabricaron todas estas herramientas y máquinas? Principalmente con otras máquinas y ensamblajes hechos en gran parte de acero, que realizan operaciones como fundición, forja, laminado, mecanizado sustractivo (torneado, fresado, vaciado y perforado), doblado, soldadura, afilado y corte. Estas últimas operaciones son posibles gracias a sorprendentes aceros para herramientas que cortan aceros al carbono tan fácilmente como un cuchillo atraviesa mantequilla blanda. Además, las máquinas que fabrican máquinas funcionan principalmente con electricidad, cuya generación (y, por ende, todo el universo de la electrónica, la informática y las telecomunicaciones) es imposible sin acero: calderas altas repletas de tubos de acero llenos de agua a presión; reactores nucleares encerrados en gruesos recipientes a presión; y vapor en expansión que hace girar grandes turbinas cuyos largos ejes se mecanizan a partir de toscas piezas forjadas de acero masivo.
El acero que permanece oculto bajo tierra incluye soportes fijos y móviles en minas profundas, además de millones de kilómetros de tuberías para exploración, revestimiento y producción en pozos de petróleo crudo y gas natural. La industria del petróleo y el gas también depende del acero enterrado cerca de la superficie (a 1–2 metros de profundidad) en tuberías de recolección, transmisión y distribución. Las líneas troncales utilizan tuberías con diámetros superiores a un metro, mientras que las líneas de distribución de gas pueden tener apenas cinco centímetros de diámetro.63 Las refinerías de petróleo crudo son, esencialmente, bosques de acero con altas columnas de destilación, craqueadores catalíticos, extensos sistemas de tuberías y depósitos de almacenamiento. Por último, cabe destacar cómo el acero salva vidas en los hospitales (desde centrífugas y máquinas de diagnóstico hasta escalpelos de acero inoxidable, ganchos quirúrgicos y retractores) y cómo también destruye: los ejércitos y flotas, con sus vastos arsenales de armas, no son más que enormes depósitos de acero dedicados a la destrucción.64
¿Podemos garantizar el suministro masivo de acero que necesitamos y qué tan significativo es su producción a nivel global? ¿Contamos con reservas suficientes de mineral de hierro para seguir produciendo acero durante muchas generaciones? ¿Podremos fabricar suficiente acero para construir infraestructuras modernas y elevar el nivel de vida en los países de bajos ingresos, donde el consumo de acero per cápita es incluso inferior al que tenían las economías prósperas hace un siglo? ¿La producción de acero es respetuosa con el medio ambiente o es excepcionalmente dañina? ¿Podemos producir este metal sin recurrir a combustibles fósiles?
La respuesta a la segunda pregunta es inequívocamente positiva. El hierro es el elemento dominante de la Tierra por masa debido a su peso (casi ocho veces más denso que el agua) y porque forma el núcleo del planeta.65 Sin embargo, también es abundante en la corteza terrestre: solo tres elementos (oxígeno, silicio y aluminio) son más comunes; el hierro, con casi un 6%, ocupa el cuarto lugar.66 La producción anual de mineral de hierro, liderada por Australia, Brasil y China, asciende actualmente a unos 2500 millones de toneladas, y los recursos mundiales superan los 800.000 millones de toneladas, que contienen cerca de 250.000 millones de toneladas de metal. Esto supone una relación recursos/producción (R/P) de más de 300 años, muy por encima de cualquier horizonte de planificación concebible (la relación R/P para el petróleo crudo es de solo 50 años).67
Además, el acero se recicla fácilmente fundiéndolo en un horno de arco eléctrico (EAF, por sus siglas en inglés): un gran contenedor cilíndrico resistente al calor, fabricado con placas pesadas de acero y revestido con ladrillos de magnesio, con una tapa desmontable en forma de cúpula, refrigerada por agua, a través de la cual se insertan tres enormes electrodos de carbono. Tras cargar el acero reciclado, los electrodos se bajan sobre él, y la corriente eléctrica que pasa a través de ellos forma un arco cuya alta temperatura (1800 °C) funde fácilmente el metal cargado.68 Sin embargo, su demanda de electricidad es enorme: incluso un moderno EAF altamente eficiente necesita tanta electricidad cada día como una ciudad estadounidense de aproximadamente 150.000 habitantes.69
El reciclaje de vehículos comienza con el drenaje de todos los fluidos, seguido de la extracción de la tapicería, baterías, servomotores, neumáticos, radios y motores funcionales, así como de componentes de plástico, caucho, vidrio y aluminio. Luego, las carrocerías despojadas se aplastan con prensas hidráulicas en preparación para ser trituradas. Con diferencia, la operación de reciclaje más desafiante es el desmantelamiento de grandes embarcaciones de navegación oceánica, que se realiza mayormente en playas de Pakistán (Gadani, al noroeste de Karachi), India (Alang, en Gujarat) y Bangladés (cerca de Chittagong). Los cascos desnudos, hechos de gruesas placas de acero, deben cortarse con sopletes de gas y plasma, un trabajo peligroso y contaminante llevado a cabo, con demasiada frecuencia, por hombres sin equipo de protección adecuado.70
Las economías prósperas ahora reciclan casi la totalidad de su chatarra automotriz, mantienen una tasa similar (>90%) para reutilizar vigas y placas de acero estructural, y tienen una tasa ligeramente inferior para el reciclaje de electrodomésticos. En los Estados Unidos, recientemente se ha reciclado más del 65% de las barras de refuerzo utilizadas en el hormigón, una proporción similar a la de latas de acero para alimentos y bebidas.71 La chatarra de acero se ha convertido en una de las mercancías de exportación más valiosas del mundo, ya que los países con una larga historia de producción de acero y abundante chatarra acumulada venden el material a productores en expansión. La Unión Europea es el mayor exportador, seguida de Japón, Rusia y Canadá; mientras que China, India y Turquía son los principales compradores.72 El acero reciclado representa casi el 30% de la producción anual total de este metal, con porcentajes nacionales que van desde el 100% en algunos pequeños productores de acero hasta casi el 70% en los Estados Unidos, alrededor del 40% en la UE y menos del 12% en China.73
Esto significa que la producción primaria de acero aún domina, generando más del doble de metal caliente cada año que el reciclado, con casi 1300 millones de toneladas en 2019. El proceso comienza con altos hornos (estructuras altas de hierro y acero revestidas con materiales resistentes al calor) que producen hierro líquido (hierro fundido o de primera fusión) al fundir mineral de hierro, coque y piedra caliza.74 El segundo paso, que consiste en reducir el alto contenido de carbono del hierro fundido para producir acero, tiene lugar en un BOF (basic oxygen furnace, u horno básico de oxígeno; el adjetivo se refiere a las propiedades químicas de la escoria producida). Este proceso fue inventado en la década de 1940 y se comercializó rápidamente después de mediados de la década de 1950.75 Los BOF actuales son grandes recipientes en forma de pera con una abertura en la parte superior, utilizados para cargar hasta 300 toneladas de hierro caliente, que luego es sometido a un chorro de oxígeno desde la parte superior e inferior. La reacción reduce el contenido de carbono del metal (hasta tan solo el 0,04%) en unos 30 minutos. La combinación de un alto horno y un horno básico de oxígeno constituye la base de la producción moderna de acero integrada. Los pasos finales incluyen la transferencia del acero caliente a máquinas de colada continua para producir planchas de acero, palanquillas (formas cuadradas o rectangulares) y tiras que finalmente se convierten en productos finales de acero.
La producción de hierro es altamente intensiva en energía, con aproximadamente el 75% de la demanda total concentrada en los altos hornos. Las mejores prácticas actuales requieren una demanda combinada de solo 17–20 gigajulios por tonelada de producto terminado; las operaciones menos eficientes necesitan entre 25 y 30 GJ/t.76 Evidentemente, el costo energético del acero secundario producido en hornos de arco eléctrico (EAF, por sus siglas en inglés) es mucho menor que el de la producción integrada: las mejores prácticas actuales apenas superan los 2 GJ/t. A esto se deben sumar los costos energéticos del laminado del metal (mayormente entre 1,5 y 2 GJ/t), de manera que las tasas globales representativas para el costo energético total pueden rondar los 25 GJ/t para la fabricación de acero integrada y los 5 GJ/t para el acero reciclado.77 El consumo energético total de la producción mundial de acero en 2019 fue de aproximadamente 34 exajulios, lo que equivale a cerca del 6% del suministro energético primario global.
Dada la dependencia de la industria en el coque de carbón y el gas natural, la fabricación de acero también ha sido un importante contribuyente a la generación antropogénica de gases de efecto invernadero. Según la World Steel Association, la tasa promedio global es de 500 kilogramos de carbono por tonelada, y la fabricación primaria de acero reciente emite alrededor de 900 megatoneladas de carbono al año, lo que representa entre el 7% y el 9% de las emisiones directas derivadas de la combustión mundial de combustibles fósiles.78 Sin embargo, el acero no es el único material importante responsable de una proporción significativa de emisiones de CO2: aunque el cemento es mucho menos intensivo en energía, debido a que su producción global es casi tres veces mayor que la del acero, su fabricación es responsable de una proporción muy similar (alrededor del 8%) de emisiones de carbono.
Hormigón: un mundo creado por el cemento
El cemento es el componente indispensable del hormigón, y se produce al calentar (a, al menos, 1450 ºC) piedra caliza molida (fuente de calcio) junto con arcilla, esquisto o materiales de desecho (fuentes de silicio, aluminio y hierro) en grandes hornos: cilindros metálicos inclinados de entre 100 y 220 metros de longitud.79 Este sinterizado a alta temperatura produce el clínker (piedra caliza fundida con aluminosilicatos), que se muele para obtener un cemento fino y pulverulento.
El hormigón está compuesto principalmente (entre el 65% y el 85%) de agregados y también de agua (entre el 15% y el 20%).80 Los agregados más finos, como la arena, generan un hormigón más resistente, pero requieren más agua en la mezcla en comparación con los agregados más gruesos, que incluyen gravas de distintos tamaños. La mezcla se cohesiona gracias al cemento, que suele representar entre el 10% y el 15% de la masa final del hormigón, y cuya reacción con el agua primero fija la mezcla y luego la endurece.
El resultado es ahora el material más ampliamente utilizado de la civilización moderna, duro, pesado y capaz de resistir décadas de uso exigente, especialmente cuando se refuerza con acero. El hormigón simple tiene una buena resistencia a la compresión (y las mejores variedades modernas son cinco veces más fuertes que las de hace dos generaciones), pero es débil frente a la tracción.81 El acero estructural tiene una resistencia a la tracción hasta 100 veces mayor, y diferentes tipos de refuerzos (mallas de acero, barras de acero, fibras de vidrio o acero, polipropileno) se han empleado para reducir esta gran brecha.
Desde 2007, la mayor parte de la humanidad vive en ciudades hechas posibles gracias al hormigón. Por supuesto, en los edificios urbanos hay muchos otros materiales: los rascacielos tienen esqueletos de acero recubiertos de vidrio o metal; las casas unifamiliares de los suburbios norteamericanos están hechas de madera (vigas, contrachapado, tableros de partículas) y placas de yeso (a menudo revestidas con ladrillo o piedra); y la madera de ingeniería se utiliza ahora para construir edificios de apartamentos de varias plantas.82 Sin embargo, los rascacielos y los altos edificios de apartamentos se apoyan en pilotes de hormigón; este material no solo se encuentra en los cimientos y sótanos, sino también en muchas paredes y techos, y es ubicuo en todas las infraestructuras urbanas: desde redes subterráneas de ingeniería (grandes tuberías, canales de cableado, alcantarillados, cimientos de metros y túneles) hasta infraestructuras de transporte en superficie (aceras, carreteras, puentes, muelles, pistas de aeropuertos). Las ciudades modernas —desde São Paulo y Hong Kong (con sus torres de apartamentos de múltiples pisos) hasta Los Ángeles y Pekín (con sus extensas redes de autopistas)— son encarnaciones del hormigón.
El cemento romano era una mezcla de yeso, cal viva y arena volcánica, y demostró ser un material excelente y duradero para grandes estructuras, incluidas las bóvedas expansivas.
El Panteón, intacto después de casi dos milenios (se completó en el año 126 d.C.), aún abarca una distancia mayor que cualquier otra estructura hecha de hormigón no reforzado.83 Sin embargo, la preparación del cemento moderno fue patentada solo en 1824 por Joseph Aspdin, un albañil inglés. Su mortero hidráulico se elaboraba al calcinar piedra caliza y arcilla a altas temperaturas: la cal, sílice y alúmina presentes en estos materiales se vitrificaban o transformaban en una sustancia similar al vidrio, cuyo molido producía el cemento Portland.84 Aspdin eligió ese nombre (todavía ampliamente utilizado hoy en día) porque, una vez endurecido y tras reaccionar con el agua, el clínker vítreo tenía un color similar al de la piedra caliza de la Isla de Portland, en el Canal de la Mancha.
Como ya se ha mencionado, el nuevo material era excelente para resistir fuerzas de compresión, y los mejores hormigones actuales pueden soportar presiones de más de 100 megapascales, lo que equivale aproximadamente al peso de un elefante africano equilibrado sobre una moneda.85 Sin embargo, la resistencia a la tracción es otro asunto: una fuerza de tracción de apenas 2 a 5 megapascales (menos de lo necesario para desgarrar la piel humana) puede romper el hormigón. Por esta razón, la adopción comercial a gran escala del hormigón en la construcción solo ocurrió después de avances graduales en el refuerzo con acero, lo que lo hizo adecuado para partes estructurales sometidas a altas tensiones.
Durante las décadas de 1860 y 1870, François Coignet y Joseph Monier, en Francia, presentaron las primeras patentes de refuerzo (Monier, un jardinero, comenzó a usar mallas de hierro para reforzar sus jardineras), pero el verdadero avance llegó en 1884 con las barras de acero de refuerzo de Ernest Ransome.86 Los primeros diseños de hornos rotatorios de cemento moderno, donde los minerales se vitrifican a temperaturas de hasta 1500 ºC, aparecieron en la década de 1890 y posibilitaron el uso asequible del hormigón en grandes proyectos. El edificio Ingalls, de dieciséis pisos en Cincinnati, se convirtió en el primer rascacielos de hormigón reforzado del mundo en 1903.87 Apenas tres años después, Thomas Edison se convenció de que el hormigón debía reemplazar a la madera en la construcción de casas unifamiliares estadounidenses y comenzó a diseñar y moldear casas de hormigón en Nueva Jersey. En 1911 intentó revivir el proyecto fallido ofreciendo también muebles baratos de hormigón, incluidos conjuntos completos de dormitorios, e incluso fabricó un fonógrafo, una de sus invenciones favoritas, con este material.88
Al mismo tiempo, en contraste con el fracaso de Edison, Robert Maillart, un ingeniero suizo, fue pionero en una tendencia de construcción con hormigón que sigue vigente: los puentes de hormigón armado, comenzando con el relativamente corto Zuoz en 1901 y el Tavanasa en 1906. Su diseño más famoso, el audaz arco Salginatobel sobre un barranco alpino, se completó en 1930 y ahora es un Monumento Internacional de Ingeniería Civil Histórica.89 Los primeros diseños de hormigón también fueron favorecidos por los arquitectos Auguste Perret en Francia (elegantes apartamentos y el Théâtre des Champs-Élysées) y Frank Lloyd Wright en Estados Unidos. Los diseños de hormigón más famosos de Wright entre guerras fueron el Hotel Imperial de Tokio, terminado justo antes del terremoto de 1923 que arrasó la ciudad y dañó la nueva estructura, y Fallingwater en Pensilvania, completado en 1939. El Museo Guggenheim en Nueva York fue su último diseño famoso en hormigón, terminado en 1959.90
La resistencia a la tracción del acero de refuerzo se mejoró aún más vertiendo el hormigón en moldes cuyas barras o cables se tensaban antes de verter el hormigón (pretensado, con anclajes que tensan el acero y se liberan una vez que el hormigón se adhiere al metal) o después de su fraguado (postensado, con tendones de acero fijados en su lugar dentro de fundas protectoras). El primer gran diseño pretensado, el Puente de Plougastel de Eugène Freyssinet, cerca de Brest, se completó en 1930.91 Con su audaz diseño blanco en forma de vela, la Ópera de Sídney de Jørn Utzon (construida entre 1959 y 1973) es quizás la estructura de hormigón pretensado más famosa del mundo.92 El pretensado es ahora común, y los puentes de hormigón armado más largos no cruzan ríos o barrancos, sino que son viaductos ferroviarios para trenes de alta velocidad. El récord lo tiene el Gran Puente Danyang–Kunshan en China (completado en 2010), que forma parte de la línea ferroviaria de alta velocidad Pekín–Shanghái, con 164,8 kilómetros de longitud.93
El hormigón armado está ahora presente en todos los edificios modernos de gran tamaño y en todas las infraestructuras de transporte, desde muelles portuarios hasta los anillos segmentados instalados por modernas tuneladoras (bajo el Canal de la Mancha y los Alpes). La configuración estándar del Sistema Interestatal de Carreteras de Estados Unidos incluye una capa de unos 28 centímetros de hormigón no armado sobre una capa de agregados naturales (piedras, grava, arena) de doble espesor —y todo el sistema interestatal contiene aproximadamente 50 millones de toneladas de cemento, 1500 millones de toneladas métricas de agregados y solo unas 6 millones de toneladas de acero (para soporte estructural y tuberías de alcantarillado).94 Las pistas de aeropuertos (de hasta 3,5 kilómetros de longitud) tienen cimientos de hormigón armado, más profundos (hasta 1,5 metros) en la zona de aterrizaje para soportar el impacto repetido de cientos de miles de aterrizajes anuales de aviones que pesan hasta 380 toneladas (el Airbus 380). Por ejemplo, la pista más larga de Canadá (4,27 kilómetros, en Calgary) requirió más de 85.000 metros cúbicos de hormigón y 16.000 toneladas de acero de refuerzo.95
Pero, con mucho, las estructuras más colosales construidas con hormigón armado son las mayores presas del mundo. La era de estas megaestructuras comenzó en la década de 1930 con la construcción de la presa Hoover en el río Colorado y la presa Grand Coulee en el río Columbia. La vertiginosa presa Hoover, situada en un desfiladero al sureste de Las Vegas, requirió unos 3,4 millones de metros cúbicos de hormigón, 20.000 toneladas de acero de refuerzo, el doble de esa cantidad en acero laminado y de tuberías, y 8000 toneladas de acero estructural.96 Cientos de estas enormes estructuras se construyeron durante la segunda mitad del siglo XX, y la mayor presa del mundo, la de Sanxia (Tres Gargantas) en el Yangzi, en China —que genera electricidad desde 2011—, cuenta con casi 28 millones de metros cúbicos de hormigón reforzado con 256.500 toneladas de acero.97
El consumo anual de cemento en Estados Unidos se multiplicó por diez entre 1900 y 1928, cuando alcanzó los 30 millones de toneladas, y el auge de la construcción en el período de posguerra —incluyendo la construcción del Sistema de Carreteras Interestatales y la ampliación de los aeropuertos del país— lo triplicó para finales de siglo. El pico se alcanzó en torno a 128 millones de toneladas en 2005, y las tasas recientes rondan los 100 millones de toneladas al año.98 Este volumen representa ahora una fracción mínima de la demanda anual en el mayor consumidor de cemento del mundo: China. En 1980, al inicio de su campaña de modernización, China producía menos de 80 millones de toneladas de cemento. En 1985 superó a Estados Unidos para convertirse en el mayor productor del mundo, y en 2019 su producción, de unos 2200 millones de toneladas, representaba algo más de la mitad del total global.99
Quizá el dato más asombroso de este ascenso es que, en solo dos años —2018 y 2019—, China produjo casi tanto cemento (unos 4400 millones de toneladas) como Estados Unidos durante todo el siglo XX (4560 millones de toneladas).
No es sorprendente que el país cuente ahora con los sistemas más extensos de autopistas, trenes de alta velocidad y aeropuertos del mundo, así como con el mayor número de grandes centrales hidroeléctricas y nuevas ciudades con millones de habitantes. Otro dato asombroso es que el mundo consume ahora en un año más cemento del que se utilizó durante toda la primera mitad del siglo XX. Y (afortunada o desafortunadamente) estas enormes masas de hormigón moderno no durarán tanto como la cúpula con casetones del Panteón.
El hormigón de construcción ordinario no es un material especialmente duradero y está expuesto a numerosos ataques ambientales.100 Las superficies expuestas sufren el embate de la humedad, la congelación, el crecimiento de bacterias y algas (especialmente en los trópicos), la deposición de ácidos y las vibraciones. Las estructuras de hormigón enterradas padecen presiones que inducen grietas, así como daños provocados por compuestos reactivos que se filtran desde la superficie. La elevada alcalinidad del hormigón (el material recién vertido tiene un pH de aproximadamente 12,5) protege eficazmente contra la corrosión del acero de refuerzo, pero las grietas y la exfoliación exponen el metal a una desintegración corrosiva.
Los cloruros atacan el hormigón sumergido en agua salada y el que se encuentra en carreteras invernales donde se utiliza sal para descongelar. Entre 1990 y 2020, el masivo hormigonado del mundo moderno ha colocado casi 700.000 millones de toneladas de material sólido, pero que se desmorona lentamente. La durabilidad de las estructuras de hormigón varía ampliamente: aunque es imposible ofrecer una cifra promedio de longevidad, muchas se deterioran gravemente tras solo dos o tres décadas, mientras que otras se mantienen en buen estado durante 60-100 años. Esto significa que, a lo largo del siglo XXI, enfrentaremos cargas sin precedentes de deterioro, renovación y eliminación del hormigón (con un problema particularmente agudo en China), ya que las estructuras tendrán que ser derribadas, para ser reemplazadas, destruidas o abandonadas.
Las estructuras de hormigón pueden ser demolidas lentamente, el acero de refuerzo puede separarse y ambos materiales pueden reciclarse: no es barato, pero sí perfectamente posible. Tras triturar y tamizar, el agregado puede incorporarse a nuevos hormigones, y el acero de refuerzo puede reciclarse.101 Incluso ahora, el hormigón de reemplazo y el nuevo hormigón son necesarios en todas partes.
En los países prósperos con bajo crecimiento poblacional, la necesidad principal es reparar infraestructuras deterioradas. El informe más reciente sobre el estado de las infraestructuras en Estados Unidos otorga calificaciones de pobres a muy pobres a todos los sectores dominados por el uso del hormigón, con presas, carreteras y aviación recibiendo una D y una calificación promedio general de apenas D+.102 Esta evaluación da una idea de lo que podría enfrentar China (en términos de volumen y costos) hacia 2050.
En contraste, los países más pobres necesitan infraestructuras esenciales, y la necesidad más básica en muchos hogares de África y Asia es reemplazar los suelos de barro por pisos de hormigón, lo que mejoraría la higiene general y reduciría la incidencia de enfermedades parasitarias en casi un 80%.103
Con poblaciones envejecidas, migración a las ciudades, globalización económica y declives regionales generalizados, una cantidad significativa de hormigón será simplemente abandonada en todo el mundo. Las ruinas de fábricas de automóviles en Detroit, las empresas abandonadas en las viejas regiones industriales de Europa y todas aquellas plantas y monumentos ahora en desuso construidos por los planificadores centrales soviéticos en la llanura rusa y Siberia son solo las primeras oleadas de esta tendencia.104 Otros ejemplos comunes y destacados de reliquias de hormigón incluyen búnkeres defensivos de gruesas paredes, como los de Normandía y la Línea Maginot, así como los silos masivos de hormigón que anteriormente albergaban misiles nucleares y que ahora permanecen vacíos en las Grandes Llanuras de América.
Perspectiva de materiales: insumos antiguos y nuevos
Durante la primera mitad del siglo XXI —con un crecimiento global de la población más lento y con cifras estancadas o incluso en declive en muchos países prósperos— las economías no deberían tener problemas para satisfacer la demanda de acero, cemento, amoníaco y plásticos, especialmente con un reciclaje más intensivo. Sin embargo, es poco probable que para 2050 todas estas industrias eliminen su dependencia de los combustibles fósiles y dejen de ser contribuyentes significativos a las emisiones globales de CO₂. Esto es particularmente improbable en los países de bajos ingresos que están en proceso de modernización, cuyas enormes necesidades de infraestructura y consumo requerirán aumentos a gran escala en todos los materiales básicos.
Replicar la experiencia de China posterior a 1990 en esos países equivaldría a un incremento de 15 veces en la producción de acero, más de 10 veces en la producción de cemento, más del doble en la síntesis de amoníaco y más de 30 veces en la producción de plásticos.105 Obviamente, incluso si otros países en proceso de modernización logran solo la mitad o incluso solo una cuarta parte de los avances materiales recientes de China, estos países aún verían multiplicaciones de sus usos actuales. Los requisitos de carbono fósil han sido —y durante décadas seguirán siendo— el precio que pagamos por los múltiples beneficios derivados de nuestra dependencia del acero, el cemento, el amoníaco y los plásticos. A medida que continuamos ampliando las conversiones de energía renovable, también necesitaremos mayores cantidades de materiales tradicionales, así como volúmenes sin precedentes de materiales que anteriormente se requerían en cantidades modestas.106
Dos ejemplos destacados ilustran esta creciente dependencia material. No hay estructuras más obvias como símbolos de generación de electricidad “verde” que los grandes aerogeneradores, pero estas enormes acumulaciones de acero, cemento y plásticos también son manifestaciones de combustibles fósiles.107 Sus bases son de hormigón armado, sus torres, góndolas y rotores son de acero (en conjunto, casi 200 toneladas por cada megavatio de capacidad instalada), y sus enormes aspas están hechas de resinas plásticas de alta intensidad energética —y difíciles de reciclar— (alrededor de 15 toneladas para un aerogenerador de tamaño medio). Todas estas partes gigantescas deben ser transportadas a los sitios de instalación en camiones de gran tamaño y erigidas por enormes grúas de acero, y las cajas de engranajes de los aerogeneradores deben lubricarse repetidamente con aceite. Multiplicar estos requerimientos por los millones de aerogeneradores necesarios para eliminar la electricidad generada a partir de combustibles fósiles demuestra cuán engañosos son los discursos sobre la inminente desmaterialización de las economías verdes.
Los coches eléctricos representan quizás el mejor ejemplo de nuevas y enormes dependencias materiales. Una batería típica de automóvil eléctrico, que pesa aproximadamente 450 kilogramos, contiene unos 11 kilogramos de litio, cerca de 14 kilogramos de cobalto, 27 kilogramos de níquel, más de 40 kilogramos de cobre y 50 kilogramos de grafito, además de unos 181 kilogramos de acero, aluminio y plásticos. Proveer estos materiales para un solo vehículo requiere procesar unas 40 toneladas de minerales, y dada la baja concentración de muchos elementos en sus minerales, implica extraer y procesar cerca de 225 toneladas de materias primas.108 Una vez más, habría que multiplicar esto por casi 100 millones de unidades, que es la producción mundial anual de vehículos de combustión interna que deberían ser reemplazados por vehículos eléctricos.
Las incertidumbres sobre las tasas futuras de adopción de vehículos eléctricos son considerables, pero una evaluación detallada de las necesidades materiales, basada en dos escenarios (suponiendo que el 25% o el 50% del parque automotor global en 2050 consistirá en vehículos eléctricos), reveló lo siguiente: de 2020 a 2050, la demanda de litio crecería entre 18 y 20 veces, la de cobalto entre 17 y 19 veces, la de níquel entre 28 y 31 veces, y se aplicarían factores de 15 a 20 para la mayoría de los demás materiales.109 Evidentemente, esto requeriría no solo una expansión drástica en la extracción y el procesamiento de litio, cobalto (gran parte del cual proviene actualmente de peligrosos pozos excavados a mano en el Congo, con amplia explotación laboral infantil) y níquel, sino también una búsqueda intensiva de nuevos recursos. Esto, a su vez, no podría llevarse a cabo sin grandes incrementos adicionales en el uso de combustibles fósiles y electricidad. Generar proyecciones optimistas sobre el aumento de la propiedad de vehículos eléctricos en el futuro es una cosa; crear estos nuevos suministros materiales a escala global masiva es otra muy distinta.
Las economías modernas siempre estarán vinculadas a flujos materiales masivos, ya sean los fertilizantes basados en amoníaco para alimentar a una población mundial que sigue creciendo; los plásticos, el acero y el cemento necesarios para nuevas herramientas, máquinas, estructuras e infraestructuras; o los nuevos insumos requeridos para producir paneles solares, turbinas eólicas, coches eléctricos y baterías de almacenamiento. Hasta que toda la energía empleada para extraer y procesar estos materiales provenga de fuentes renovables, la civilización moderna seguirá dependiendo fundamentalmente de los combustibles fósiles utilizados en la producción de estos materiales indispensables. Ninguna inteligencia artificial, ninguna aplicación y ningún mensaje electrónico cambiarán esta realidad.
Notas:
1. El primer producto comercial que utilizó transistores fue una radio Sony en 1954; el primer microprocesador fue el 4004 de Intel en 1971; el primer ordenador personal ampliamente utilizado fue el Apple II, lanzado en 1977, seguido por el IBM PC en 1981, y IBM presentó el primer smartphone en 1992.
2. P. Van Zant, Microchip Fabrication: A Practical Guide to Semiconductor Processing (Nueva York: McGraw-Hill Education, 2014). Para costos energéticos, véase M. Schmidt et al., “Life cycle assessment of silicon wafer processing for microelectronic chips and solar cells,” International Journal of Life Cycle Assessment 17 (2012), pp. 126–144.
3. Semiconductor and Materials International, “Silicon shipment statistics” (2020), https://www.semi.org/en/products-services/market-data/materials/si-shipment-statistics.
4. V. Smil, Making the Modern World: Materials and Dematerialization (Chichester: John Wiley, 2014); Smil, “What we need to know about the pace of decarbonization.” Para más información sobre el costo energético de los materiales, véase T. G. Gutowski et al., “The energy required to produce materials: constraints on energy-intensity improvements, parameters of demand,” Philosophical Transactions of the Royal Society A 371 (2013), 20120003.
5. Los totales anuales de la producción nacional y global de todos los metales y minerales no metálicos de importancia comercial están disponibles en actualizaciones regulares publicadas por el US Geological Survey. La edición más reciente es: US Geological Survey, Mineral Commodity Summaries 2020, https://pubs.usgs.gov/periodicals/mcs2020/mcs2020.pdf.
6. J. P. Morgan, Mountains and Molehills: Achievements and Distractions on the Road to Decarbonization (Nueva York: J. P. Morgan Private Bank, 2019).
7. Estos son cálculos aproximados propios, basados en una producción anual de 1,8 Gt de acero, 4,5 Gt de cemento, 150 Mt de NH3 y 370 Mt de plásticos.
8. Smil, “What we need to know about the pace of decarbonization.” Para una visión optimista de las posibilidades de descarbonización de sectores difíciles de mitigar, véase Energy Transitions Commission, Mission Possible.
9. M. Appl, Ammonia: Principles & Industrial Practice (Weinheim: Wiley-VCH, 1999); Smil, Enriching the Earth.
10. Science History Institute, “Roy J. Plunkett,” https://www.sciencehistory.org/historical-profile/roy-j-plunkett.
11. Para más detalles, véase V. Smil, Grand Transitions: How the Modern World Was Made (Nueva York: Oxford University Press, 2021).
12. Para la historia de los cambios globales en el uso de la tierra, véase HYDE, History Database of the Global Environment (2010), http://themasites.pbl.nl/en/themasites/hyde/index.html.
13. Florida y Carolina del Norte aún producen más del 75 por ciento de la roca fosfórica estadounidense, que ahora representa alrededor del 10 por ciento de la producción mundial: USGS, “Phosphate rock” (2020), https://pubs.usgs.gov/periodicals/mcs2020/mcs2020-phosphate.pdf.
14. Smil, Enriching the Earth, pp. 39–48.
15. W. Crookes, The Wheat Problem (Londres: John Murray, 1899), pp. 45–46.
16. Para los precursores del descubrimiento de Haber y para descripciones detalladas de sus experimentos de laboratorio, véase Smil, Enriching the Earth, pp. 61–80.
17. Para la vida y obra de Carl Bosch, véase K. Holdermann, Im Banne der Chemie: Carl Bosch Leben und Werk (Düsseldorf: Econ-Verlag, 1954).
18. En ese momento, la proporción de fertilizantes nitrogenados inorgánicos en el suministro agrícola de China era de no más del 2 por ciento: Smil, Enriching the Earth, p. 250.
19. V. Pattabathula y J. Richardson, “Introduction to ammonia production,” CEP (septiembre de 2016), pp. 69–75; T. Brown, “Ammonia technology portfolio: optimize for energy efficiency and carbon efficiency,” Ammonia Industry (2018); V. S. Marakatti y E. M. Giagneaux, “Recent advances in heterogeneous catalysis for ammonia synthesis,” ChemCatChem (2020).
20. V. Smil, China’s Past, China’s Future: Energy, Food, Environment (Londres: RoutledgeCurzon, 2004), pp. 72–86.
21. Para más detalles sobre el proceso de amoníaco de M. W. Kellogg, véase Smil, Enriching the Earth, pp. 122–130.
22. FAO, http://www.fao.org/faostat/en/#search/Food%20supply%20kcal%2Fcapita%2Fday.
23. L. Ma et al., “Modeling nutrient flows in the food chain of China,” Journal of Environmental Quality 39/4 (2010), pp. 1279–1289. La proporción de la India también es igual de alta: H. Pathak et al., “Nitrogen, phosphorus, and potassium in Indian agriculture,” Nutrient Cycling in Agroecosystems 86 (2010), pp. 287–299.
24. Siempre me divierte ver otra lista de los inventos más importantes (o los mayores) de la era moderna que incluye ordenadores, reactores nucleares, transistores o automóviles… y siempre omite la síntesis de amoníaco.
25. El consumo anual de carne per cápita (peso de la canal) es un buen indicador de estas diferencias: los promedios recientes han sido de aproximadamente 120 kg en Estados Unidos, 60 kg en China y solo 4 kg en India: http://www.fao.org/faostat/en/#data/FBS.
26. El poder quitamanchas del amoníaco lo convierte en un ingrediente favorito. Windex, el líquido limpiaventanas más común en América del Norte, contiene un 5% de NH3.
27. J. Sawyer, “Understanding anhydrous ammonia application in soil” (2019), https://crops.extension.iastate.edu/cropnews/2019/03/understanding-anhydrous-ammonia-application-soil.
28. Yara Fertilizer Industry Handbook.
29. Asia oriental y meridional (dominadas, respectivamente, por China e India) consumen ahora un poco más del 60% de toda la urea: Nutrien, Fact Book 2019, https://www.nutrien.com/sites/default/files/uploads/2019-05/Nutrien%20Fact%20Book%202019.pdf.
30. El promedio global de absorción del nitrógeno aplicado por los cultivos (eficiencia del uso de fertilizantes) disminuyó entre 1961 y 1980 (del 68% al 45%), y desde entonces se ha estabilizado en aproximadamente el 47%: L. Lassaletta et al., “50 year trends in nitrogen use efficiency of world cropping systems: the relationship between yield and nitrogen input to cropland,” Environmental Research Letters 9 (2014), 105011.
31. J. E. Addicott, The Precision Farming Revolution: Global Drivers of Local Agricultural Methods (Londres: Palgrave Macmillan, 2020).
32. Calculado a partir de datos en: http://www.fao.org/faostat/en/#data/RFN.
33. Europa aplica ahora 3,5 veces más nitrógeno por hectárea de tierras de cultivo que África, y las diferencias entre las tierras más intensamente fertilizadas de la UE y las tierras de cultivo más pobres del África subsahariana son más de diez veces mayores: http://www.fao.org/faostat/en/#data/RFN.
34. Algunas reacciones comunes de polimerización—procesos de conversión de moléculas más simples (monómeros) en redes tridimensionales más largas—requieren solo una masa ligeramente mayor del insumo inicial: 1,03 unidades de etileno son necesarias para producir 1 unidad de polietileno de baja densidad (cuyo uso más común es en bolsas plásticas), y la misma proporción se aplica a la conversión de cloruro de vinilo en policloruro de vinilo (PVC, común en productos sanitarios). P. Sharpe, “Making plastics: from monomer to polymer,” CEP (septiembre de 2015).
35. M. W. Ryberg et al., Mapping of Global Plastics Value Chain and Plastics Losses to the Environment (París: UNEP, 2018).
36. The Engineering Toolbox, “Young’s Modulus—Tensile and Yield Strength for Common Materials” (2020), https://www.engineeringtoolbox.com/young-modulus-d_417.html.
37. El Boeing 787 fue el primer avión de pasajeros construido predominantemente con materiales compuestos: por volumen constituyen el 89% del avión y por peso el 50%, con un 20% de aluminio, 15% de titanio y 10% de acero: J. Hale, “Boeing 787 from the ground up,” Boeing AERO 24 (2006), pp. 16–23.
38. W. E. Bijker, Of Bicycles, Bakelites, and Bulbs: Toward a Theory of Sociotechnical Change (Cambridge, MA: The MIT Press, 1995).
39. S. Mossman, ed., Early Plastics: Perspectives, 1850–1950 (Londres: Science Museum, 1997); S. Fenichell, Plastic: The Making of a Synthetic Century (Nueva York: HarperBusiness, 1996); R. Marchelli, The Civilization of Plastics: Evolution of an Industry Which has Changed the World (Pont Canavese: Sandretto Museum, 1996).
40. N. A. Barber, Polyethylene Terephthalate: Uses, Properties and Degradation (Haupaugge, NY: Nova Science Publishers, 2017).
41. P. A. Ndiaye, Nylon and Bombs: DuPont and the March of Modern America (Baltimore, MD: Johns Hopkins University Press, 2006).
42. R. Geyer et al., “Production, use, and fate of all plastic ever made,” Science Advances 3 (2017), e1700782.
43. Y no solo todo tipo de pequeños objetos de plástico: también los suelos, divisores de habitaciones, baldosas de techo, puertas y marcos de ventanas pueden ser de plástico.
44. Aquí tienes una revisión exhaustiva sobre las carencias de EPI en Estados Unidos: S. Gondi et al., “Personal protective equipment needs in the USA during the COVID-19 pandemic,” The Lancet 390 (2020), e90–e91. Y aquí solo uno de los numerosos reportajes en medios: Z. Schlanger, “Begging for Thermometers, Body Bags, and Gowns: U.S. Health Care Workers Are Dangerously Ill-Equipped to Fight COVID-19,” Time (20 de abril de 2020). Para una perspectiva global, véase World Health Organization, “Shortage of personal protective equipment endangering health workers worldwide” (3 de marzo de 2020).
45. C. E. Wilkes and M. T. Berard, PVC Handbook (Cincinnati, OH: Hanser, 2005).
46. M. Eriksen et al., “Plastic pollution in the world’s oceans: More than 5 trillion plastic pieces weighing over 250,000 tons afloat at sea,” PLoS ONE 9/12 (2014) e111913. Y aquí la explicación de por qué la mayoría de ellas no son plásticas: G. Suaria et al., “Microfibers in oceanic surface waters: A global characterization,” Science Advances 6/23 (2020).
47. Gráficos y tablas básicas que resumen la clasificación del acero y del hierro fundido están disponibles en: https://www.mah.se/upload/_upload/steel%20and%20cast%20iron.pdf.
48. Para la larga historia del hierro fundido, véase V. Smil, Still the Iron Age: Iron and Steel in the Modern World (Ámsterdam: Elsevier, 2016), pp. 19–31.
49. Para detalles sobre los métodos premodernos de producción de acero en Japón, China, India y Europa, véase Smil, Still the Iron Age, pp. 12–17.
50. Las resistencias a compresión del granito y del acero alcanzan los 250 megapascales (MPa), pero la resistencia a tracción del granito no supera los 25 MPa frente a los 350–750 MPa de los aceros de construcción: Cambridge University Engineering Department, Materials Data Book (2003), http://www-mdp.eng.cam.ac.uk/web/library/enginfo/cueddatabooks/materials.pdf.
51. Para un tratamiento más detallado, véase J. E. Bringas, ed., Handbook of Comparative World Steel Standards (West Conshohocken, PA: ASTM International, 2004).
52. M. Cobb, The History of Stainless Steel (Materials Park, OH: ASM International, 2010).
53. Council on Tall Buildings and Human Habitat, “Burj Khalifa” (2020), http://www.skyscrapercenter.com/building/burj-khalifa/3.
54. The Forth Bridges, “Three bridges spanning three centuries” (2020), https://www.theforthbridges.org/.
55. D. MacDonald and I. Nadel, Golden Gate Bridge: History and Design of an Icon (San Francisco: Chronicle Books, 2008).
56. “Introduction of Akashi-Kaikyō Bridge,” Bridge World (2005), https://www.jb-honshi.co.jp/english/bridgeworld/bridge.html.
57. J. G. Speight, Handbook of Offshore Oil and Gas Operations (Ámsterdam: Elsevier, 2011).
58. Smil, Making the Modern World, p. 61.
59. World Steel Association, “Steel in Automotive” (2020), https://www.worldsteel.org/steel-by-topic/steel-markets/automotive.html.
60. International Association of Motor Vehicle Manufacturers, “Production Statistics” (2020), http://www.oica.net/production-statistics/.
61. Nippon Steel Corporation, “Rails” (2019), https://www.nipponsteel.com/product/catalog_download/pdf/K003en.pdf.
62. Para la historia de los barcos portacontenedores, véase V. Smil, Prime Movers of Globalization (Cambridge, MA: MIT Press, 2010), pp. 180–194.
63. U.S. Bureau of Transportation Statistics, “U.S. oil and gas pipeline mileage” (2020), https://www.bts.gov/content/us-oil-and-gas-pipeline-mileage.
64. Los tanques de batalla principales son las armas de acero más pesadas desplegadas a gran escala por los ejércitos modernos: la versión más grande del tanque estadounidense M1 Abrams (casi completamente de acero) pesa 66,8 toneladas.
65. D. Alfè et al., “Temperature and composition of the Earth’s core,” Contemporary Physics 48/2 (2007), pp. 63–68.
66. Sandatlas, “Composition of the crust” (2020), https://www.sandatlas.org/composition-of-the-earths-crust/.
67. US Geological Survey, “Iron ore” (2020), https://pubs.usgs.gov/periodicals/mcs2020/mcs2020-iron-ore.pdf.
68. A. T. Jones, Electric Arc Furnace Steelmaking (Washington, DC: American Iron and Steel Institute, 2008).
69. Un horno de arco eléctrico (EAF) que consuma solo 340 kWh/t de acero tiene una potencia de 125–130 MW, y su operación diaria (40 cargas de 120 t) requerirá 1,63 GWh de electricidad. Utilizando el promedio anual de consumo eléctrico de un hogar en EE. UU., de aproximadamente 29 kWh/día y un tamaño promedio de 2,52 personas por hogar, esto equivale a unos 56.000 hogares o 141.000 personas.
70. “Alang, Gujarat: The World’s Biggest Ship Breaking Yard & A Dangerous Environmental Time Bomb,” Marine Insight (marzo de 2019), https://www.marineinsight.com/environment/alang-gujarat-the-world’s-biggest-ship-breaking-yard-a-dangerous-environmental-time-bomb/. En marzo de 2020, la vista satelital de Google mostró más de 70 embarcaciones y plataformas de perforación en varias etapas de desmantelamiento en las playas de Alang, entre P. Rajesh Shipbreaking en el extremo sur y Rajendra Shipbreakers, a unos 10 km al noroeste.
71. Concrete Reinforcing Steel Institute, “Recycled materials” (2020), https://www.crsi.org/index.cfm/architecture/recycling.
72. Bureau of International Recycling, World Steel Recycling in Figures 2014–2018 (Brussels: Bureau of International Recycling, 2019).
73. World Steel Association, Steel in Figures 2019 (Brussels: World Steel Association, 2019).
74. Para la larga historia de los altos hornos, véase V. Smil, Still the Iron Age. Para la construcción y operación de altos hornos modernos, véase M. Geerdes et al., Modern Blast Furnace Ironmaking (Ámsterdam: IOS Press, 2009); I. Cameron et al., Blast Furnace Ironmaking (Ámsterdam: Elsevier, 2019).
75. La invención y difusión de los hornos básicos de oxígeno se describe en W. Adams y J. B. Dirlam, “Big steel, invention, and innovation,” Quarterly Journal of Economics 80 (1966), pp. 167–189; T. W. Miller et al., “Oxygen steelmaking processes,” en D. A. Wakelin, ed., The Making, Shaping and Treating of Steel: Ironmaking Volume (Pittsburgh, PA: The AISE Foundation, 1998), pp. 475–524; J. Stubbles, “EAF steelmaking—past, present and future,” Direct from MIDREX 3 (2000), pp. 3–4.
76. World Steel Association, “Energy use in the steel industry” (2019), https://www.worldsteel.org/en/dam/jcr:f07b864c-908e-4229-9f92-669f1c3abf4c/fact_energy_2019.pdf.
77. Para tendencias históricas, véase V. Smil, Still the Iron Age; US Energy Information Administration, “Changes in steel production reduce energy intensity” (2016), https://www.eia.gov/todayinenergy/detail.php?id=27292.
78. World Steel Association, Steel’s Contribution to a Low Carbon Future and Climate Resilient Societies (Brussels: World Steel Association, 2020); H. He et al., “Assessment on the energy flow and carbon emissions of integrated steelmaking plants,” Energy Reports 3 (2017), pp. 29–36.
79. J. P. Saxena, The Rotary Cement Kiln: Total Productive Maintenance, Techniques and Management (Boca Raton, FL: CRC Press, 2009).
80. V. Smil, “Concrete facts,” Spectrum IEEE (marzo de 2020), pp. 20–21; National Concrete Ready Mix Associations, Concrete CO2 Fact Sheet (2008).
81. F.-J. Ulm, “Innovationspotenzial Beton: Von Atomen zur Grünen Infrastruktur,” Beton- und Stahlbetonbauer 107 (2012), pp. 504–509.
82. Los edificios modernos de madera se han ido haciendo más altos, pero no utilizan madera sin tratar, sino madera laminada cruzada (CLT, por sus siglas en inglés), un material patentado de ingeniería prefabricado a partir de varias capas (3, 5, 7 o 9) de madera secada en horno, colocadas de forma plana y pegadas entre sí: https://cwc.ca/how-to-build-with-wood/wood-products/mass-timber/cross-laminated-timber-clt/. En 2020, el edificio de CLT más alto del mundo (85,4 m) fue Mjøstårnet, diseñado por Voll Arkitekter en Brumunddal, Noruega, una estructura multipropósito (apartamentos, un hotel, oficinas, un restaurante, una piscina) completada en 2019: https://www.dezeen.com/2019/03/19/mjostarne-worlds-tallest-timber-tower-voll-arkitekter-norway/.
83. F. Lucchini, Pantheon—Monumenti dell’Architettura (Roma: Nuova Italia Scientifica, 1966).
84. A. J. Francis, The Cement Industry, 1796–1914: A History (Newton Abbot: David and Charles, 1978).
85. Smil, “Concrete facts.”
86. J.-L. Bosc, Joseph Monier et la naissance du ciment armé (París: Editions du Linteau, 2001); F. Newby, ed., Early Reinforced Concrete (Burlington, VT: Ashgate, 2001).
87. American Society of Civil Engineers, “Ingalls building” (2020), https://www.asce.org/project/ingalls-building/; M. M. Ali, “Evolution of Concrete Skyscrapers: from Ingalls to Jin Mao,” Electronic Journal of Structural Engineering 1 (2001), pp. 2–14.
88. M. Peterson, “Thomas Edison’s Concrete Houses,” Invention & Technology 11/3 (1996), pp. 50–56.
89. D. P. Billington, Robert Maillart and the Art of Reinforced Concrete (Cambridge, MA: MIT Press, 1990).
90. B. B. Pfeiffer and D. Larkin, Frank Lloyd Wright: The Masterworks (Nueva York: Rizzoli, 1993).
91. E. Freyssinet, Un amour sans limite (París: Editions du Linteau, 1993).
92. Sydney Opera House: Utzon Design Principles (Sídney: Sydney Opera House, 2002).
93. History of Bridges, “The World’s Longest Bridge—Danyang–Kunshan Grand Bridge” (2020), http://www.historyofbridges.com/famous-bridges/longest-bridge-in-the-world/.
94. US Geological Survey, “Materials in Use in U.S. Interstate Highways” (2006), https://pubs.usgs.gov/fs/2006/3127/2006-3127.pdf.
95. Associated Engineering, “New runway and tunnel open skies and roads at Calgary International Airport” (June 2015).
96. Entre muchos libros sobre la presa Hoover, destacan los relatos de testigos oculares contenidos en: A. J. Dunar y D. McBride, Building Hoover Dam: An Oral History of the Great Depression (Las Vegas: University of Nevada Press, 2016).
97. Power Technology, “Three Gorges Dam Hydro Electric Power Plant, China” (2020), https://www.power-technology.com/projects/gorges/.
98. Los datos sobre la producción, comercio y consumo de cemento en Estados Unidos están disponibles en los resúmenes anuales publicados por el US Geological Survey. La edición de 2020: US Geological Survey, Mineral Commodity Summaries 2020, https://pubs.usgs.gov/periodicals/mcs2020/mcs2020.pdf.
99. A 320 millones de toneladas, la producción de India en 2019, la segunda más grande del mundo, es solo el 15 por ciento del total chino: USGS, “Cement” (2020), https://pubs.usgs.gov/periodicals/mcs2020/mcs2020-cement.pdf.
100. N. Delatte, ed., Failure, Distress and Repair of Concrete Structures (Cambridge: Woodhead Publishing, 2009).
101. D. R. Wilburn y T. Goonan, Aggregates from Natural and Recycled Sources (Washington, DC: USGS, 2013).
102. American Society of Civil Engineers, 2017 Infrastructure Report Card, https://www.infrastructurereportcard.org/.
103. C. Kenny, “Paving Paradise,” Foreign Policy (enero/febrero de 2012), pp. 31–32.
104. Las estructuras de concreto abandonadas en todo el mundo incluyen ahora casi cualquier tipo de edificio, desde bases de submarinos nucleares hasta reactores nucleares (cada uno de estos se puede encontrar en Ucrania), pasando por estaciones de ferrocarril, grandes estadios deportivos, teatros y monumentos.
105. Calculado a partir de datos oficiales chinos publicados anualmente en el China Statistical Yearbook del país. La última edición está disponible en: http://www.stats.gov.cn/tjsj/ndsj/2019/indexeh.htm.
106. M. P. Mills, Mines, Minerals, and “Green” Energy: A Reality Check (Nueva York: Manhattan Institute, 2020).
107. V. Smil, “What I see when I see a wind turbine,” IEEE Spectrum (marzo de 2016), p. 27.
108. H. Berg y M. Zackrisson, “Perspectives on environmental and cost assessment of lithium metal negative electrodes in electric vehicle traction batteries,” Journal of Power Sources 415 (2019), pp. 83–90; M. Azevedo et al., Lithium and Cobalt: A Tale of Two Commodities (Nueva York: McKinsey & Company, 2018).
109. C. Xu et al., “Future material demand for automotive lithium-based batteries,” Communications Materials 1 (2020), p. 99.
Sobre el autor:
Vaclav Smil es Profesor Distinguido Emérito en la Universidad de Manitoba. Es autor de más de cuarenta libros sobre temas como la energía, el cambio ambiental y demográfico, la producción de alimentos y la nutrición, la innovación técnica, la evaluación de riesgos y las políticas públicas. Su obra más reciente para Penguin, Numbers Don’t Lie, se publicó en más de veinte idiomas. Ningún otro científico vivo ha tenido más libros (sobre una amplia variedad de temas) reseñados en la prestigiosa revista científica Nature. Miembro de la Real Sociedad de Canadá, en 2010 fue reconocido por Foreign Policy como uno de los 100 pensadores globales más influyentes.
* Artículo original: “Understanding Our Material World: The Four Pillars of Modern Civilization”. Capítulo del libro ‘How The World Really Works. A Scientist’s Guide to Our Past, Present and Future’. Traducción: ‘Hypermedia Magazine’.
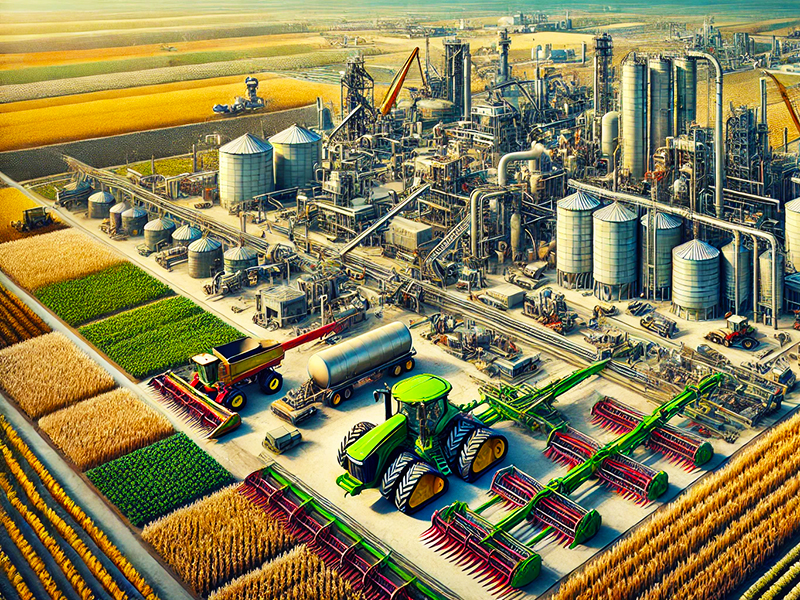
Comemos combustibles fósiles
Por Vaclav Smil
Ninguna transformación reciente ha sido tan fundamental, como nuestra capacidad para producir, año tras año, un excedente de alimentos.